Process mapping dates back to the early flow process chart by Frank and Lillian Gilbreth which they unveiled in 1921 as part of his propheticallytitled talk Process Charts—First Steps in Finding the One Best Way They introduced it by saying "Every detail of a process is more or less affected by every other detail;Processes and expectations in place to prevent the S&OP process from bogging down, or drifting into unproductive, unfocused efforts BE AN S&OP LEADER Because you are the champion of the team tasked with implementing the S&OP process, you must research what happened previously You have to ask questions to find answersTherefore the entire process must be presented in such
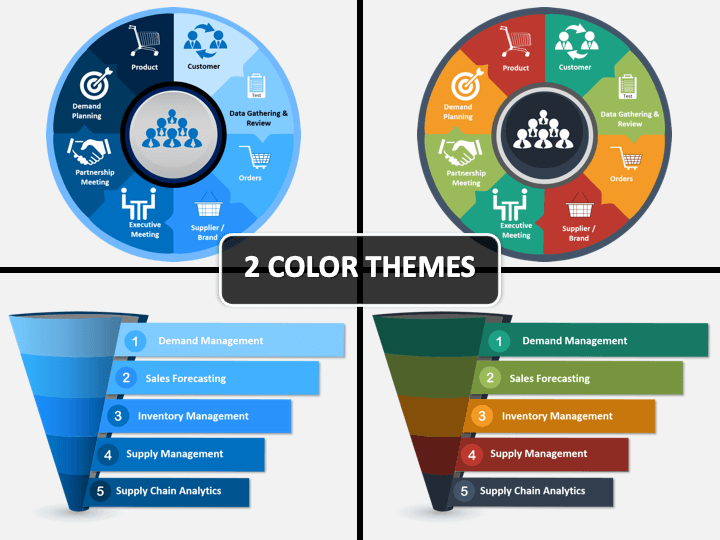
Sales And Operations Planning Powerpoint Template Sketchbubble
Sop process mapping
Sop process mapping-Mechanisms for process mapping, levels at which it can be applied, and the roles and responsibilities of process owners 1030 Exercise 1 Feedback 1045 Break 1100 Mapping Processes The stages involved in mapping processes including how to construct a SIPOC chart 1145 Exercise 2 Mapping A Process In a previous post, I talked about the ineffectiveness of Excel, ERP, and legacy planning for




Mindmap For Sales Operations Planning 2 0 Supply Chain Movement
Process maps are used for communication and education/training in most projects, too Developing an accurate process map is more than a "conferenceroom" activity Tapping into team members' knowledge of the process is a good place to start gathering input for the map, but directly observing the process in operation also is important Process/operation symbols Process mapping is an incredibly effective tool for improving operational efficiency and offers a broad range of organizational benefits To get the most out of it, try ProcessMaker's industry leading lowcode intelligent BPM software Easily create enterprisegrade business processes and leverage ProcessMakerS&OP facilitator helps discover why opinions differ while keeping the S&OP process on track S&OP Silos Potential silo conflicts outside of the S&OP process that hinder S&OP performance conflicts of interest, such as one department lowering its costs by offloading expenses onto another department failure to share information, or
According to IBF, S&OP is a process that coordinates different areas of the business to meet customer demand with the appropriate level of supply When establishing your process, it is important to consider who will be responsible for each step of the process You will also want to set expectations for handoffs, meetings, and how you willBusiness process mapping is a way to visualize what a business does by taking into account roles, responsibilities and standards Business process modeling (BPM) takes this one step further by providing a visual way to understand, analyze, and improve upon a current method of working There are a number of reasons why organizations map theirCreating accurate and useful process maps requires considerable time and resources, but these maps are vital to any meaningful operations management process evaluation and improvement effort Here's some advice for creating an accurate process map Always ask why While constructing an initial process map, find out why certain actions are being done In many cases,
The process map is a tool that graphically shows the inputs, actions and outputs of a process in a clear, stepbystep map of the process This is tollgate # 3 of Define in the DMAICThe purpose of process mapping is to help team members and othersSales and operations planning (S&OP) is an integrated business management process through which the executive/leadership team continually achieves focus, alignment and synchronization among all functions of the organizationThe S&OP process includes an updated forecast that leads to a sales plan, production plan, inventory plan, customer lead time (backlog) plan, new product Sales and Operations Planning (S&OP) Sales and operations planning (S&OP) is a business management process where leadership and executive teams meet to ensure each business function is aligned to balance supply and demand S&OP requires crossorganizational collaboration to create detailed forecasts for predicted sales



1
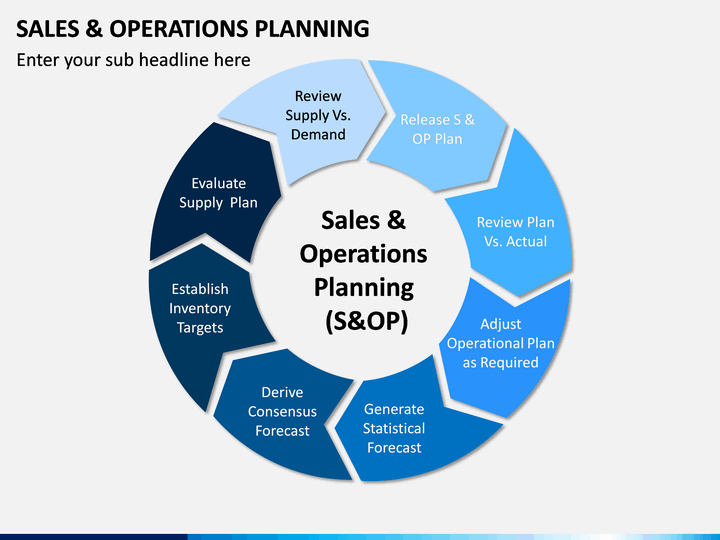



Sales And Operations Planning Powerpoint Template Sketchbubble
During S&OP Vendor Day 21 Evelien Busschers, Supply Chain Management Consultant at Involvation, presented their solutions in a breakout session 'S&OP Subway Map A journey from Strategy to Schedule' Sales & Operations Planning and the moreFind local businesses, view maps and get driving directions in Google MapsThe Forecast Phase page and its subpages are visible to user groups S&OP Commercial Sales Managers and S&OP Process Coordinator Data




The 5 Most Common Sales Operations Planning Mistakes And How To Avoid Them Supply Chain 24 7




Sales And Operations Planning Powerpoint Presentation Slides Presentation Powerpoint Templates Ppt Slide Templates Presentation Slides Design Idea
The Pareto rule applies here – in the S&OP process (both in its implementation and in its leadership) that 80% of success in S&OP depends on the people involved, 15% of the data and 5% of the hardware or software used People then, are what will make S&OP happen – the data and hardware are secondaryA process map is a planning and management tool that visually describes the flow of work Using process mapping software, process maps show a series of events that produce an end resultA process map is also called a flowchart, process flowchart, process chart, functional process chart, functional flowchart, process model, workflow diagram, business flow diagram or processInformative video describing the S&OP Process as it relates to SAP IBP Krypt, Inc is your consulting partner for implementing SAP IBP
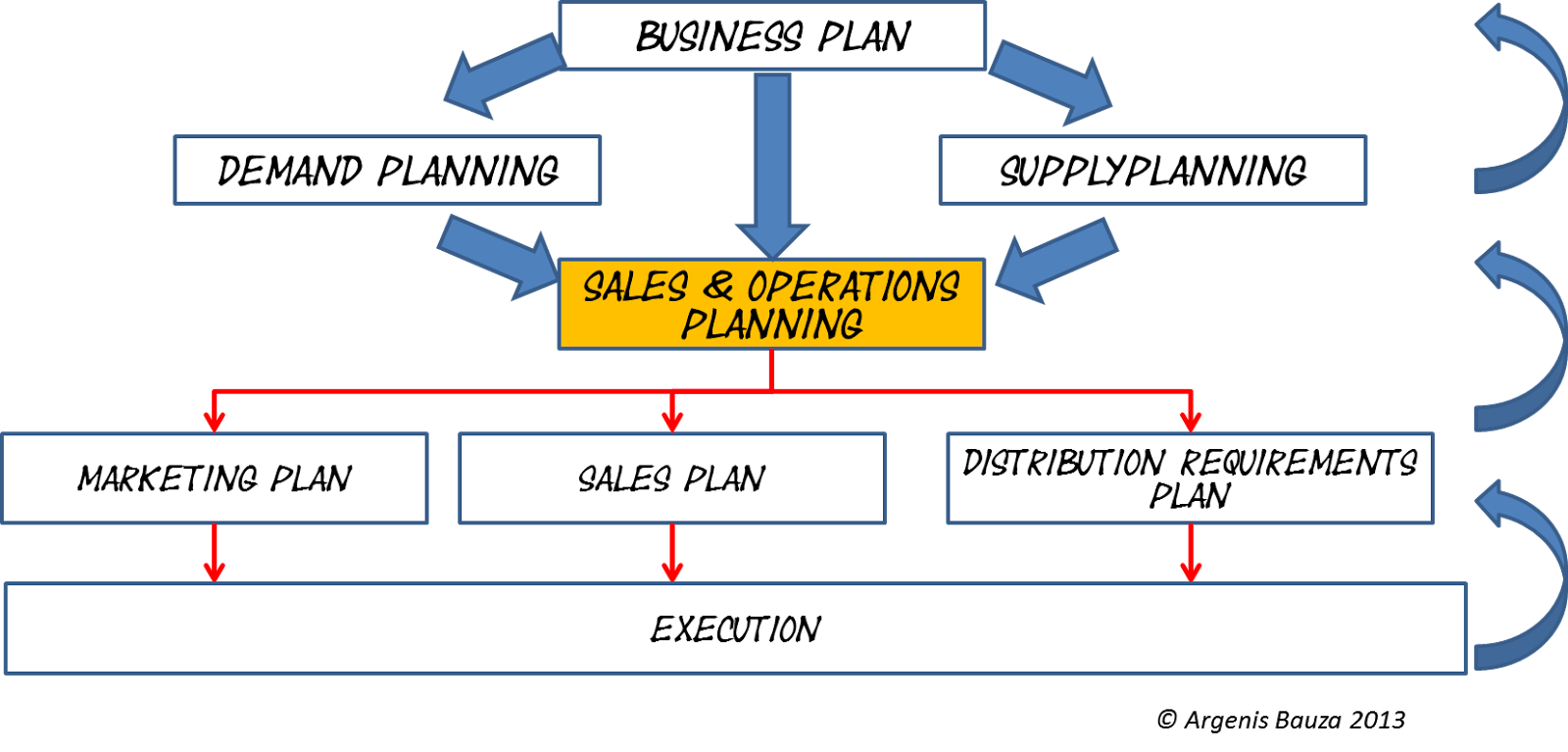



My Business Ideas Notebook June 13




What Is S Op How S Op Works Demand Planning Com
No Yes Is it capable? S&OP gives management the ability to direct its business to achieve a sustainable competitive advantage The overall objective of S&OP is to arrive at a business "Game Plan" to help manage and allocate critical resources to meet the needs of the customer at the lowest cost S&OP is a fivestep process as illustrated in Figure 1The four buttons in the first row control the four phases in the S&OP process Each phase must go in sequence If the button to begin a phase is clicked out of sequence, a warning message appears Start Forecast;
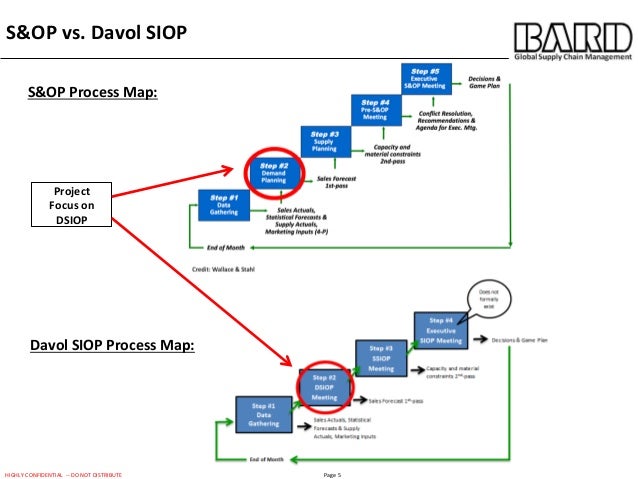



Dsiop Process Review




Mindmap For Sales Operations Planning 2 0 Supply Chain Movement
Process Map Symbols Each step in a process is represented by a shape in a process map These shapes are also called flowchart shapes There are nearly 30 standard shapes that you can use in process mappingHowever, we think for most people, using a handful of the most common shapes will be easier to understandProcess mapping consists of a collection of tools and methods used to understand an organization and its processes Those tools allow us to document, analyze, improve, streamline and redesign business processes to realize organizational efficiencies A process map is aNo Yes Perform root cause analysis Map and implement the "tobe" process Collect Data Is the
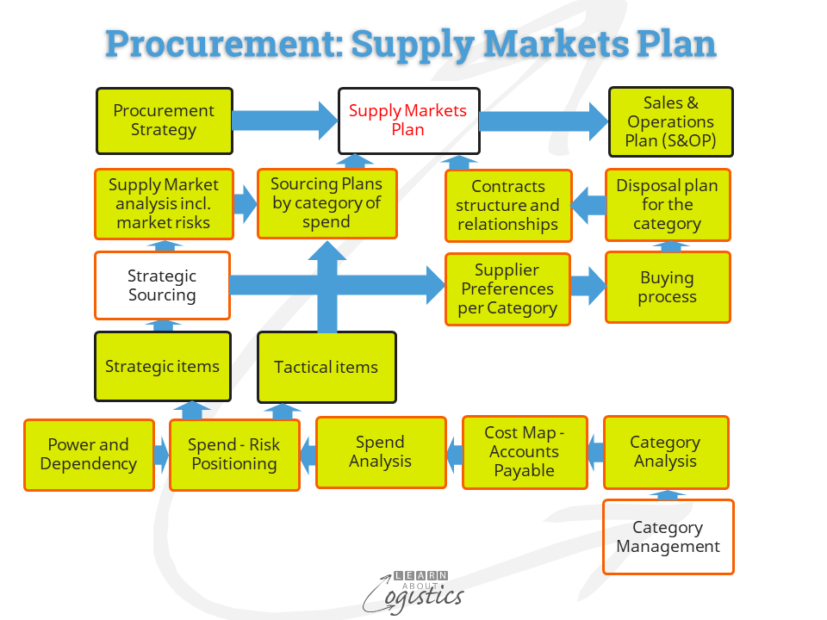



Supply Markets Plan Is A Supply Chain Input To The S Op Learn About Logistics




Blogs
S&OP Challenges Challenges Senior leadership support & "walk the talk" Achieving process compliance Identifying S&OP Champion or expert to lead implementation Clear definition and acceptance of roles and responsibilities, including defining specific objectives in employee appraisals Establishing S&OP meetings as the business priorityProcess Mapping Tools and Techniques Basic Components of Business Process Mapping •Process The overall workflow from a starting point to its successful completion •Tasks or Activities Something performed by a person or a system •Flows This is indicated on the process map by connecting lines and arrows •EventsThe operation times and distances moved are also recorded along the symbols side Flow process chart are of three types Man, Machine and Material These charts are shown in Figs 1, 184 and 185 The man type flow process chart shows the process from the point of view of man/operator It indicates the activities of man throughout the process




S Op Five Steps To Get Started Supply Chain Shaman




What Is S Op How S Op Works Demand Planning Com
Process mapping is the first key step aimed at identifying and documenting tasks or activities within a business process It details an endtoend process, including what is being done, who is involved, as well as when and where Process mapping aids in supporting business process modeling, which is intended to be a tool to maximizeGIB customer portal Request a demo GIB (Juan Ignacio Camino, Álvaro FernándezNovel, Javier Ocaña and Pablo Díaz) There are four different techniques to assists process analysis and design FLOWCHARTS, TIME FUNCTION MAPPING, PROCESS CHARTS, VALUE STREAM MAPPING, and SERVICE BLUEPRINTING 4G1 Flowchart Definition A flow chart is a graphical or symbolic
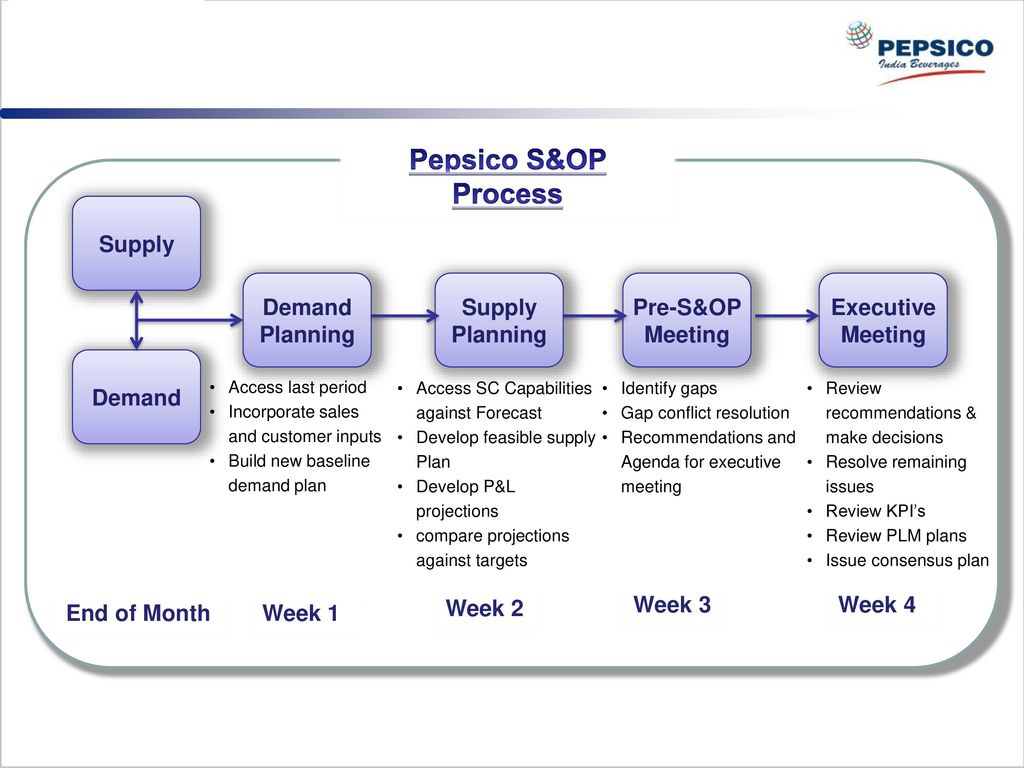



S Op Process Challenges In Beverage Industry Ppt Video Online Download




From Chaos To Control July 1 08 Cscmp S Supply Chain Quarterly
If you're introducing a new process at your workplace or documenting an existing one, a process map template can help A process flow chart template uses symbols and diagrams to depict complex processes from start to finish Just enter your process data to the Excel flowchart template, then export to automatically create the shapes and connectors that visually tell the storyApplication process components The outofthe box S&OP application supports these process steps 2 Review and update annual plan if applicable 1 Create S&OP instance 9 Rebalance demand to supply • Review the supply plan and its ability to support the demand plan • Collaboratively review the impact of proposed resolutions 11 End S&OP cycle 3 Start S&OP cycle2/22/15 Primary FlowS&OP, or sales & operations planning, is a monthly integrated business management process that empowers leadership to focus on key supply chain drivers, including sales, marketing, demand management, production, inventory management, and new product introduction With an eye on financial and business impact, the goal of S&OP software is to




Mindmap For S Op And Ibp Supply Chain Movement




The S Op And The 3 Different Levels Of General Planning Based On Apics Download Scientific Diagram
Process Mapping Asimple"approach"to"improvement" by"making"a"process"visible An"article"by"Dr"Mike"Bell"CSci,"CChem,"FRSC Simple"Improvement"Ltd mikebell@si8couk wwwsimpleimprovementcouk wwwsimpleimprovementcouk info@simpleimprovementcouk !Page 1 of 11 Process Mapping A simple approach toSteps to S&OP There are two distinct phases to S&OP 1) process design, and 2) process conduct In the design phase, all of the technical workings are engineered, and in the conduct phase S&OP is used as a business management process The following 10 steps describe how to go about these two phases Steps 15 are design and steps 610 are There are many Six Sigma tools that are covered in Lean Six Sigma Green Belt trainingOne of the most important processes of the Six Sigma Define phase of the DMAIC cycle is Process MappingProcess mapping is one of the fundamental Six Sigma principles that are shortly covered in free Six Sigma coursesBut let's start at the beginning and ask the most important
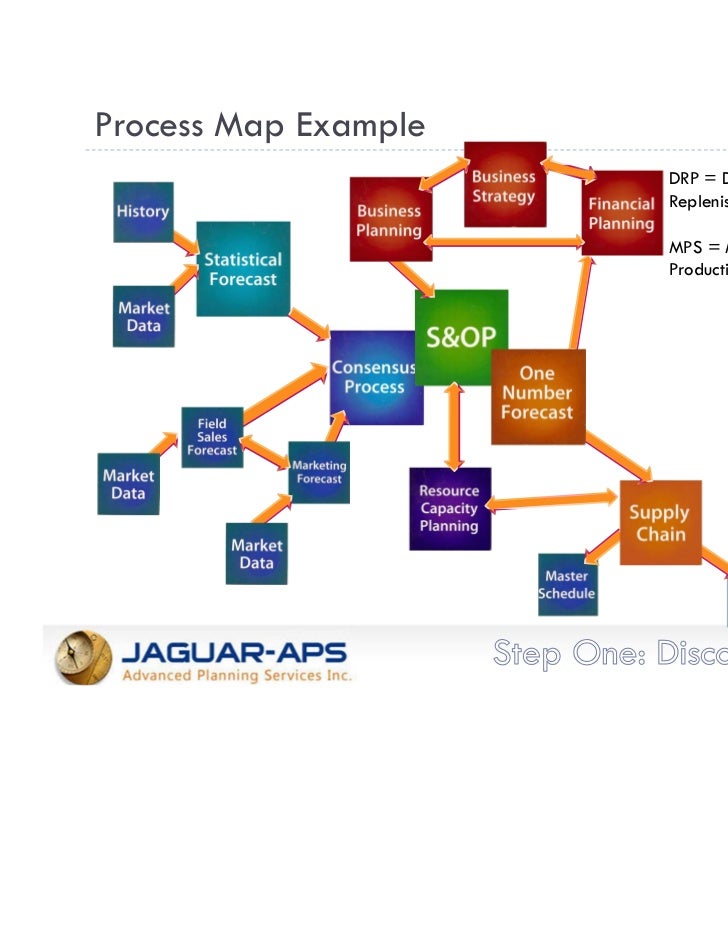



Isf Conference Prague 11 S Op Process Overview




3 Primary Components Of Sales Operations Planning People Process And Technology Supply Chain 24 7
S&OP Process Mapping Select the process Get the right people together Establish process boundaries List steps, activities and decisions Map the "asis" process Simplify the process Collect Data Is the process stable? Process maps are investments in an organization's understanding of how the business model works, along with plans to continue to improve that work in the future Process maps can be very versatile, with many capabilities and uses They are very visual and contain about ten main standard symbols When done right, there is very little deviationProcess maps detail the flow of work needed to complete a task These maps are visual representations of a process A process map may detail something simple, like




Five Ways To Upgrade Your Business Planning Process With Advanced Analytics 18 07 24 Supplychainbrain



Getting To Grips With Sales And Operational Planning Bloor Research
Sales and operations planning (S&OP) is a popular process that aligns a company's diverse functions while balancing supply and demand S&OP gives executives a comprehensive overview of the business so they can grasp where it stands (in all its complexity) This allows them to continuously match highlevel strategy with daytoday operationalSales & Operations Planning (S&OP) is the process by which we bring together all the plans for the business (Customers, Sales, Marketing, Development, Manufacturing, Sourcing, and Financial) into one integrated set of tactical plans S&OP gives management the ability to direct its business to achieve a sustainable competitive advantageThere is a planning process that is Business process mapping, a part of Business Process Management (BPM), is a framework used to create visual representations of work processesBusiness process maps show the relationship between the steps and inputs to produce an endproduct or service, such as when a product goes through packaging or when an employee's leave is approved
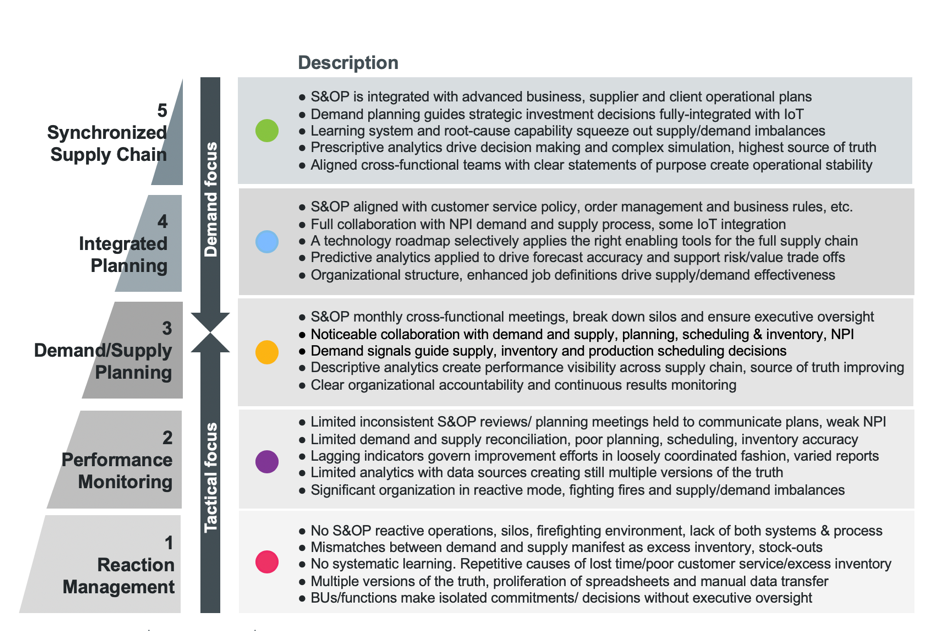



Sales Operations Planning Engagement Model Tvo Maine Pointe




S Op Implementation Roadmap




Mindmap For S Op And Ibp Supply Chain Movement



A Comprehensive Overview Of Sales And Operations Planning S Op



1




23 S Op Ideas Sales And Operations Planning Supply Chain How To Plan
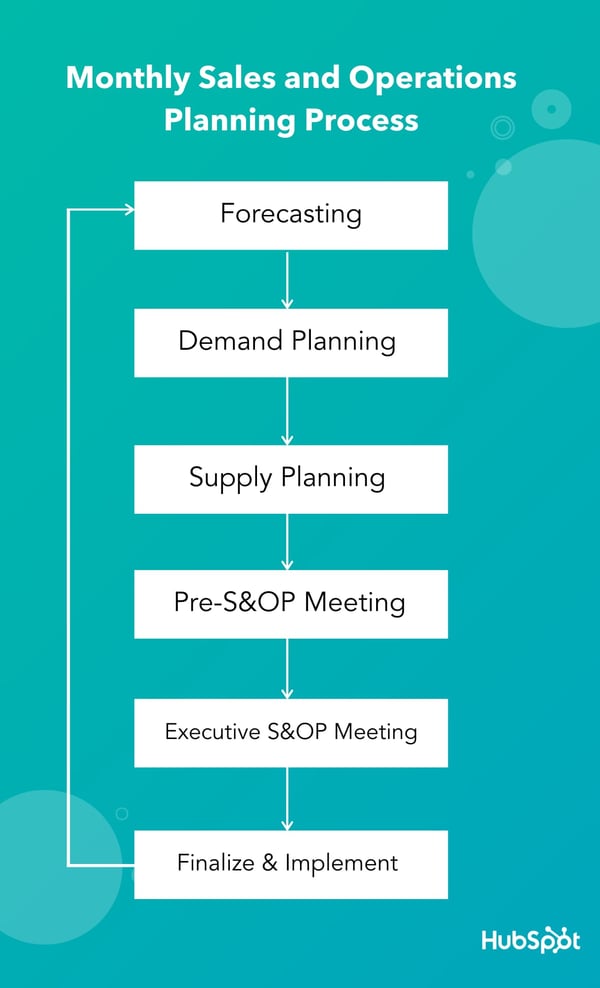



A Comprehensive Overview Of Sales And Operations Planning S Op
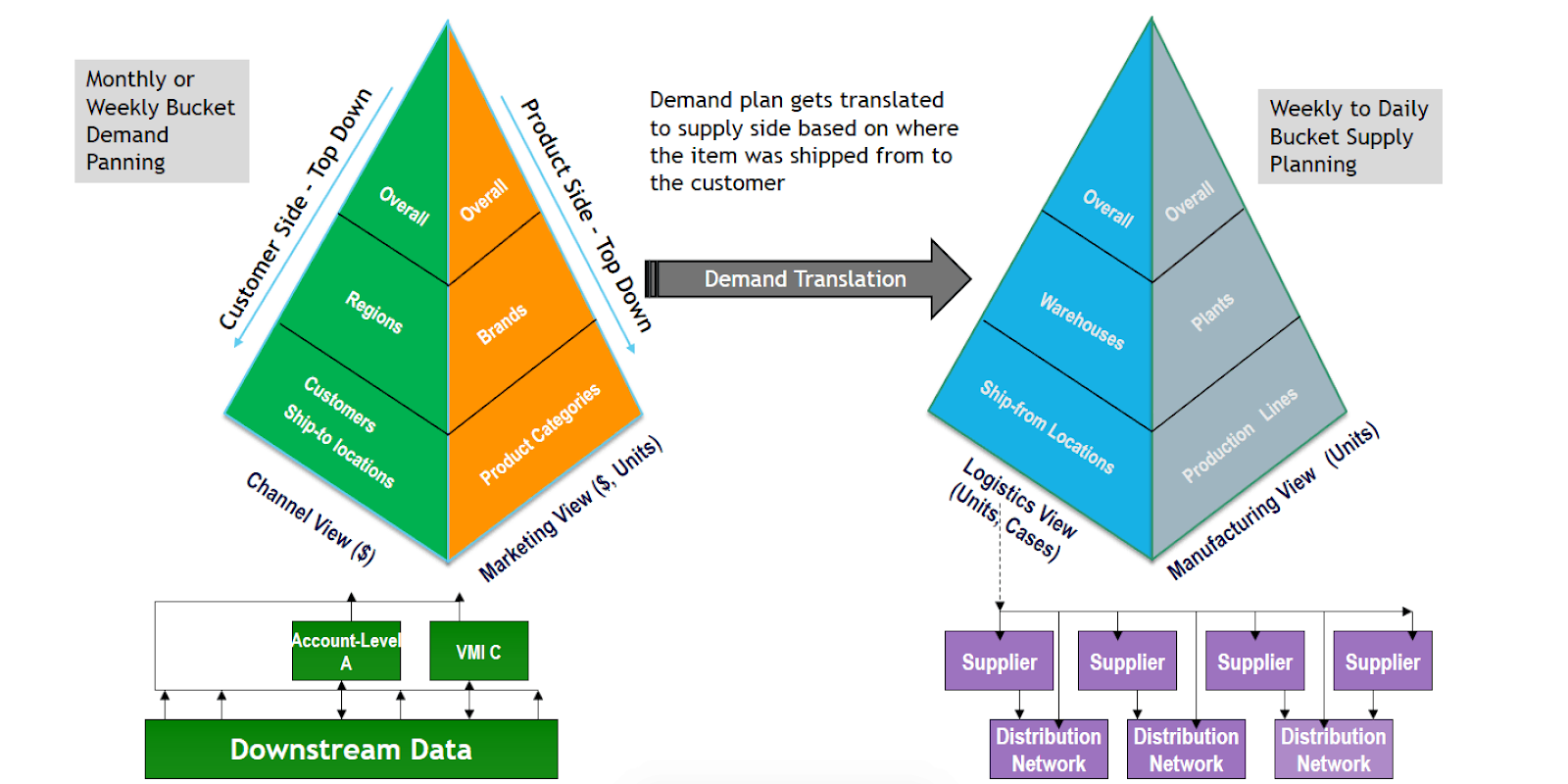



Supply Planning Processes Options Analytics Oh My Plex Demandcaster




Sales And Operations Planning Powerpoint Presentation Slides Presentation Powerpoint Templates Ppt Slide Templates Presentation Slides Design Idea
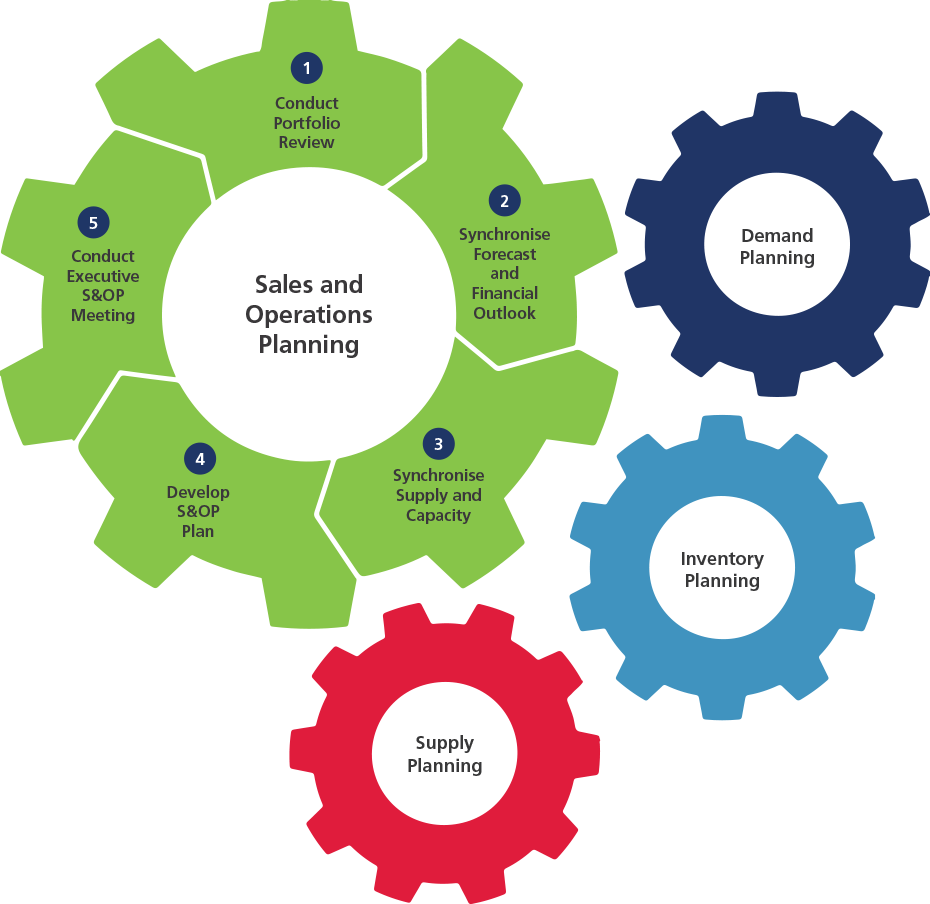



S Op Made Practical The European Business Review




The Fully Integrated S Op Of A Multi Site System In Supply Chain Download Scientific Diagram




23 S Op Ideas Sales And Operations Planning Supply Chain How To Plan
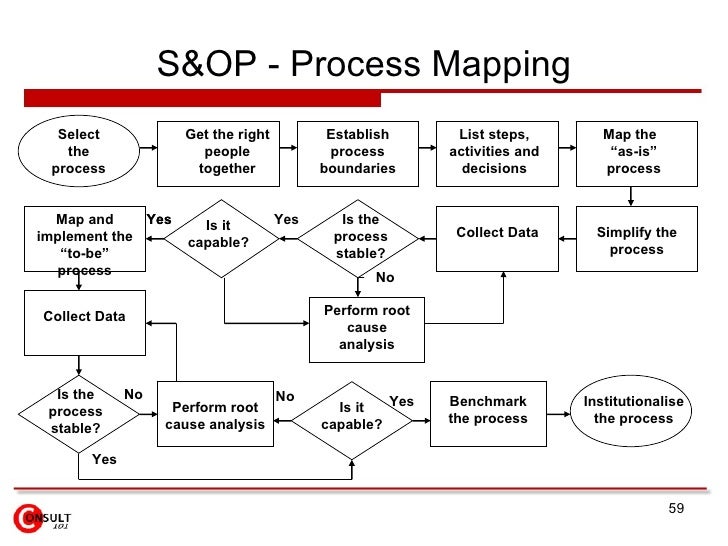



Snap S Op Process Photos On Pinterest
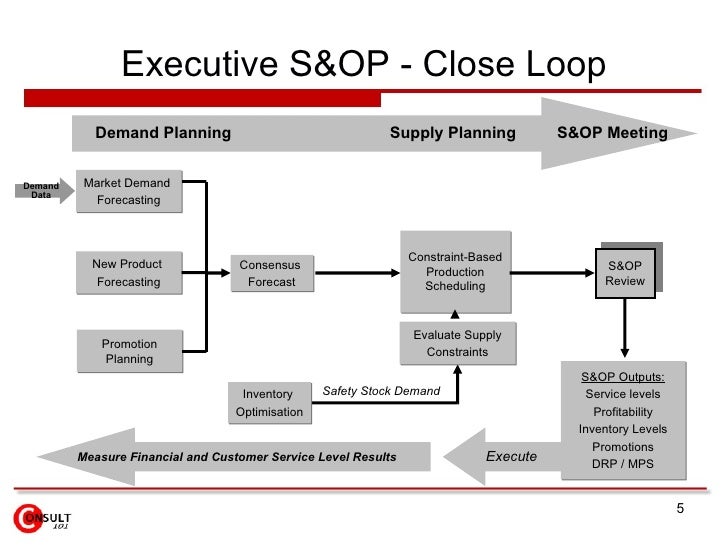



S Op Implementation Roadmap




S Op A Vision For The Future The Expert Interview Series 1 Supply Chain Trend




Sap Sales And Operations Planning Software Product Xsop Pdf Free Download



2




Achieve Excellence In Sales And Operations Planning Sapinsider




Mindmap Sales Operations Planning S Op Supply Chain Movement
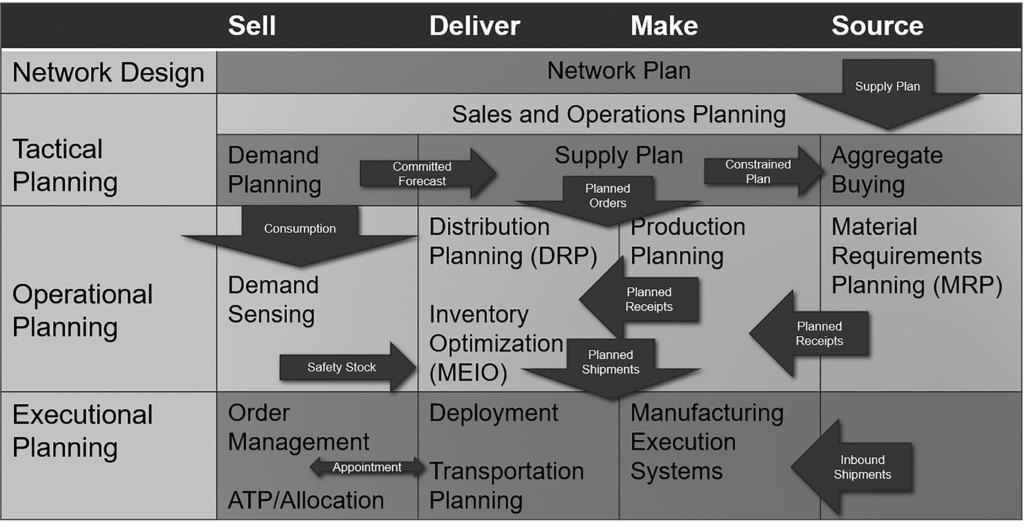



Is S Op Excellence Slip Slidin Away Supply Chain Shaman
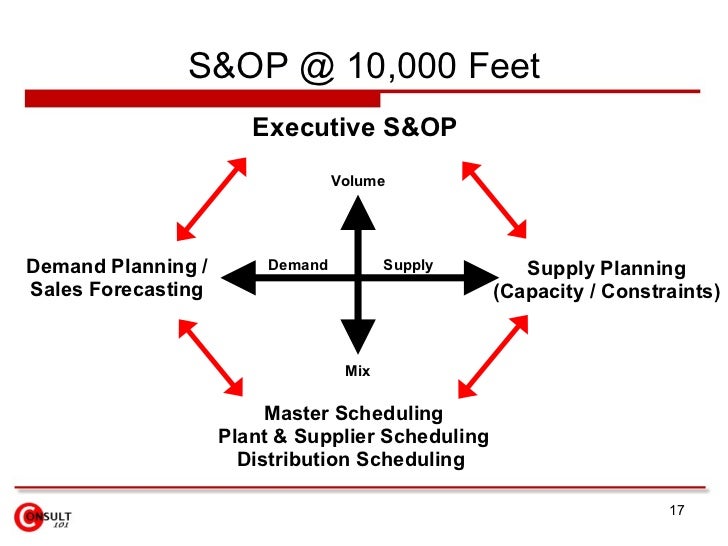



S Op Process



Supply Chain Graphic Of The Week The S Op Process



S Op Sales And Operations Planning And Sco




What Is S Op How S Op Works Demand Planning Com
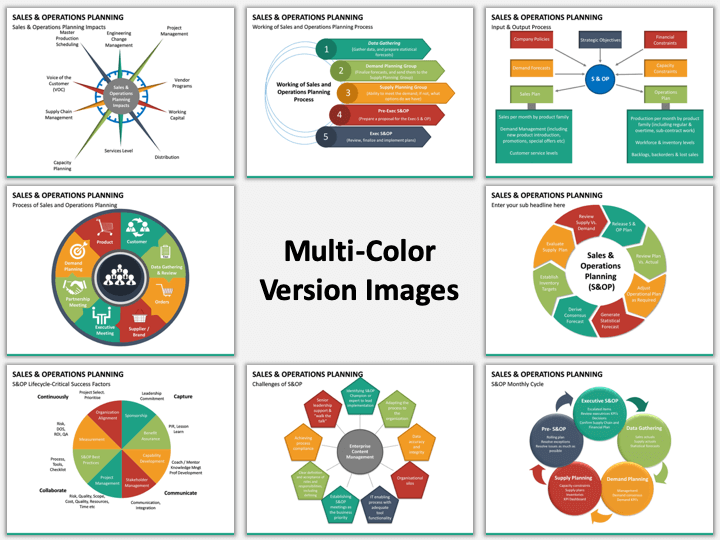



Sales And Operations Planning Powerpoint Template Sketchbubble




Mindmap For S Op And Ibp Supply Chain Movement




Achieve Excellence In Sales And Operations Planning Sapinsider




Achieve Excellence In Sales And Operations Planning Sapinsider
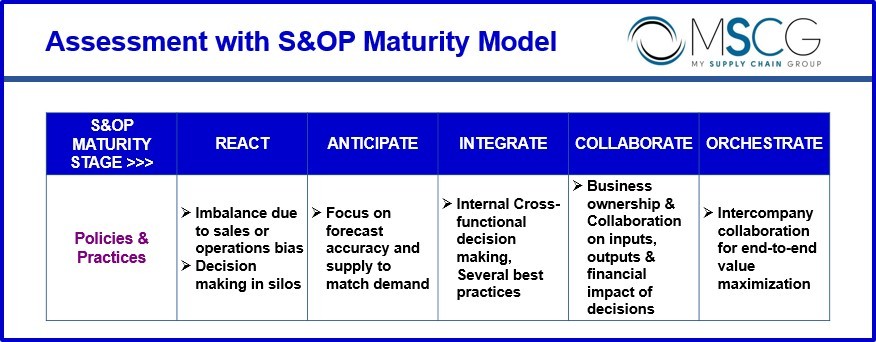



Road Map Of Integrated Business Planning For Supply Chain Part Ii The 5 Ps Of S Op Maturity My Supply Chain Group




S Op Heuristics Flow Chart Download Scientific Diagram



2




S Op Application Flow At A Glance Sc Navigator



Enterra Insights Nine Technologies Transforming The Supply Chain Part 2
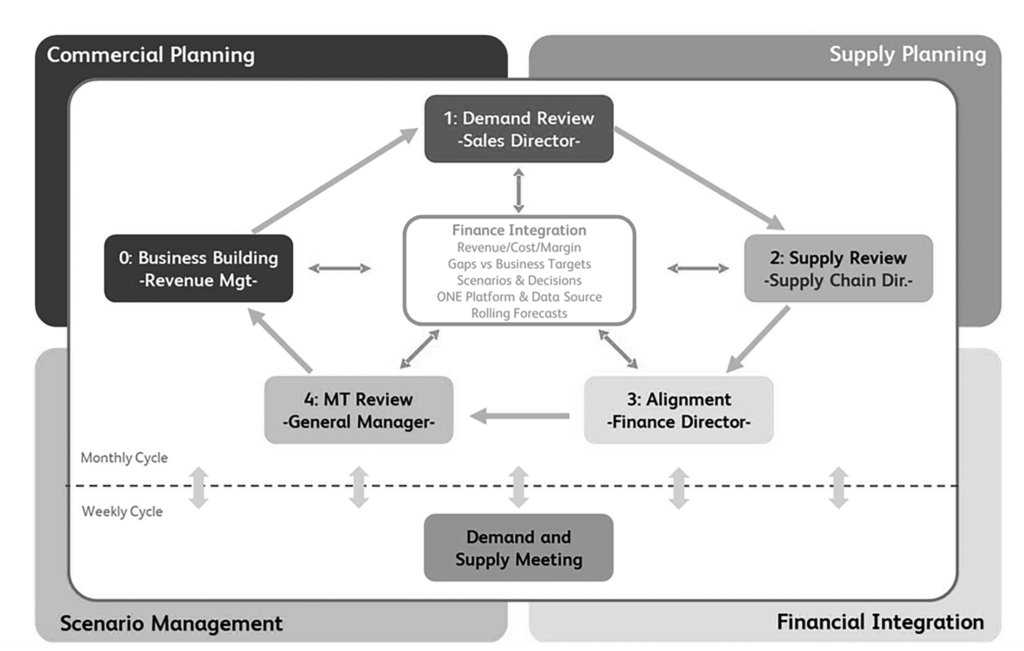



Is S Op Excellence Slip Slidin Away Supply Chain Shaman




The Lost Link To Make Strategy Work Sales Operations Planning S Op Strategok By Javier Go Sales And Operations Planning Business Architecture Strategies




Solution Framework Of S Op In The Supply Chain Download Scientific Diagram
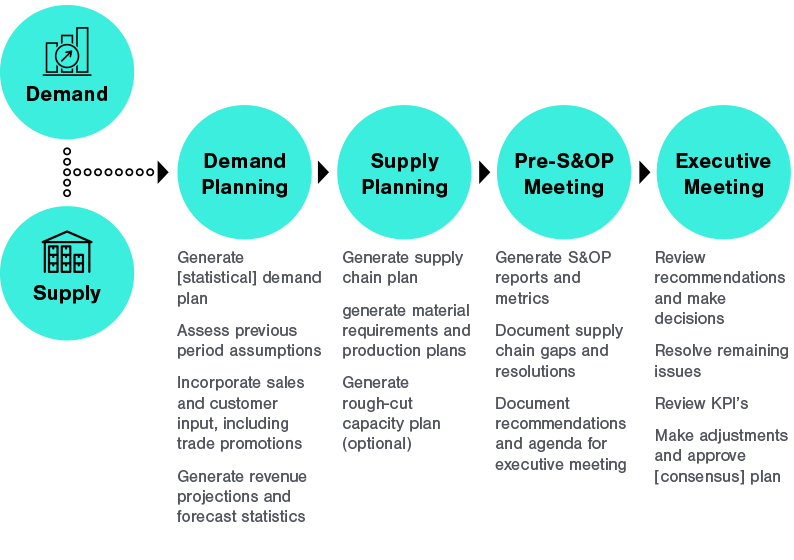



Implementing A Sales Operations Planning S Op Process Plex Demandcaster




Sales And Operations Planning S Op 101 Smartsheet




S Op 360
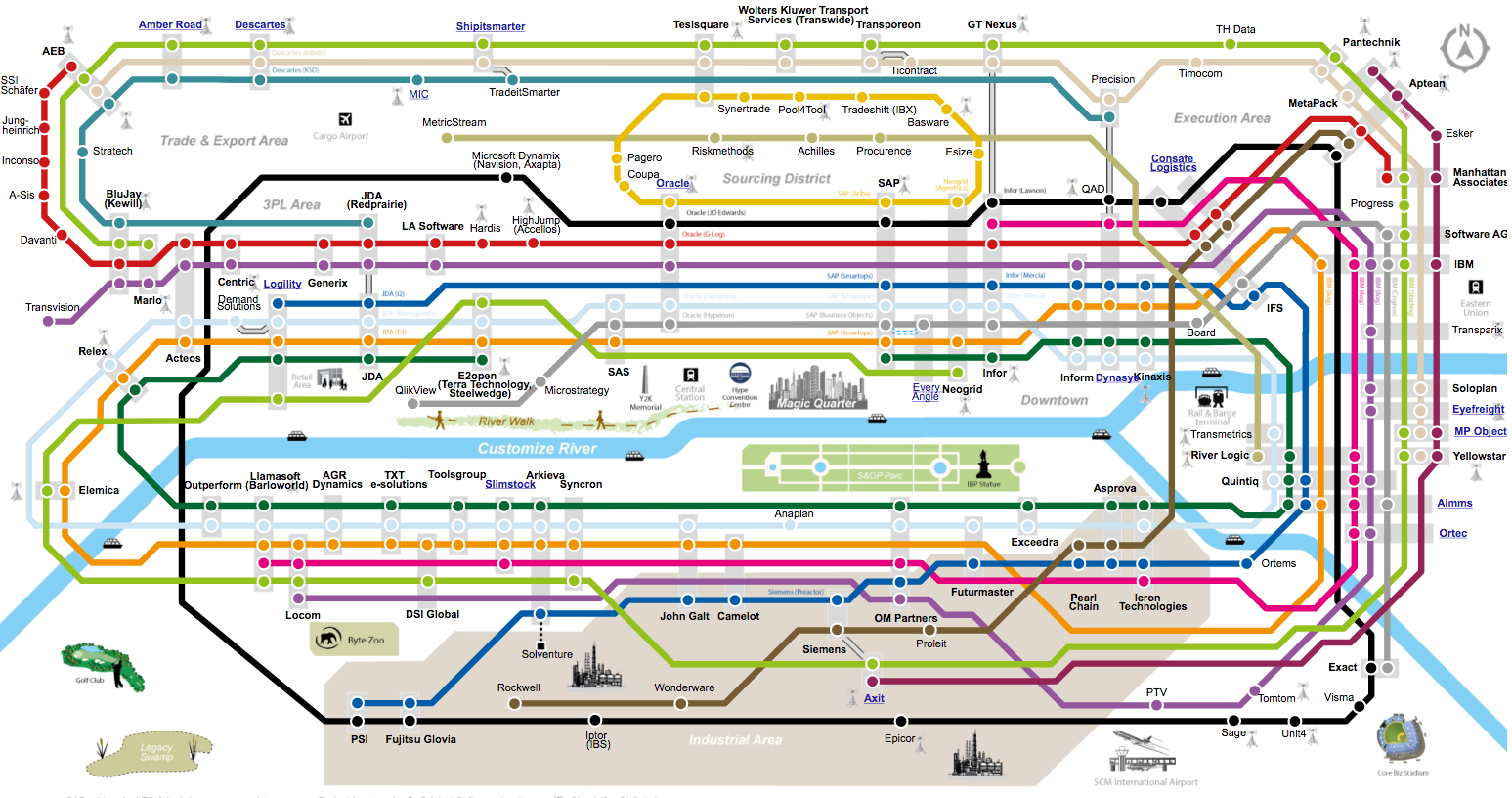



Aimms Featured In It Subway Map Of European Supply Chain Software Providers Aimms




Monthly S Op Process Sales And Operations Planning Wikipedia Sales And Operations Planning Best Apps For Teachers Apps For Teachers




Integrating The S Op Process The Planning Blog
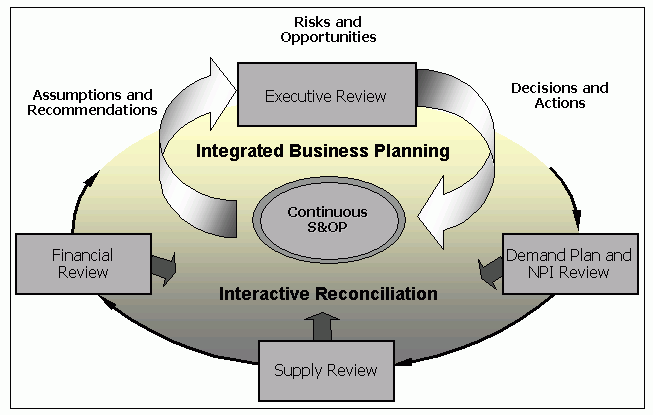



Oracle Demantra Sales And Operations Planning User Guide




S Op Heuristics Flow Chart Download Scientific Diagram



Framework For Measuring Performance Of The Sales And Operations Planning Process Emerald Insight



2
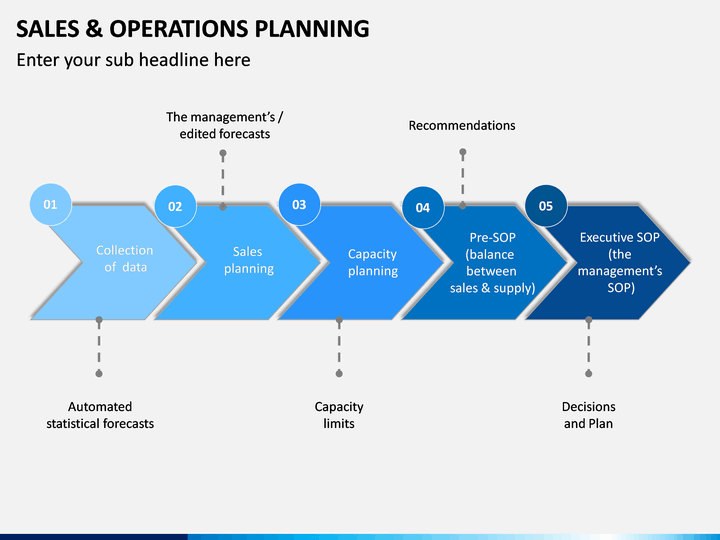



Sales And Operations Planning Powerpoint Template Sketchbubble
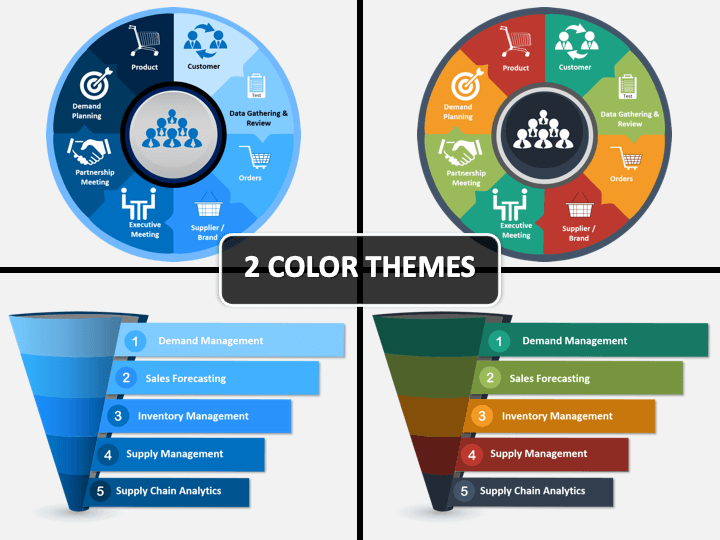



Sales And Operations Planning Powerpoint Template Sketchbubble
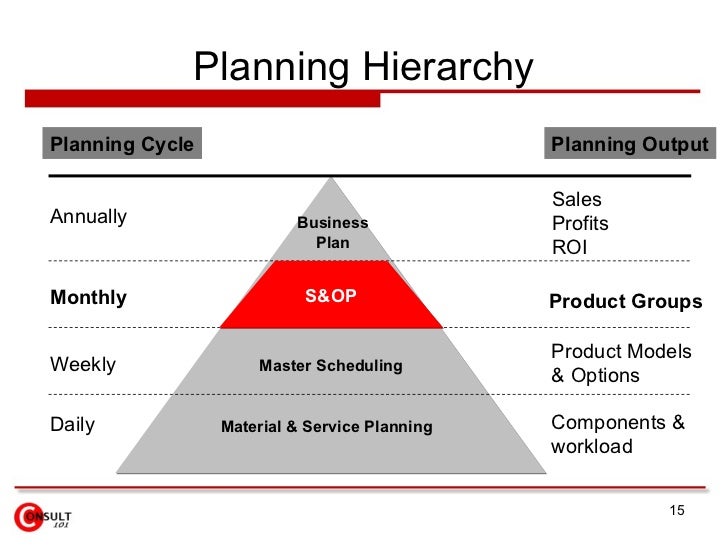



S Op Process




What Is One Plan S Op Arkieva



S Op Sales And Operations Planning And Sco




Sales And Operations Planning In Manufacturing Manage Collaboration Across The Entire Organization Tompkins Solutions
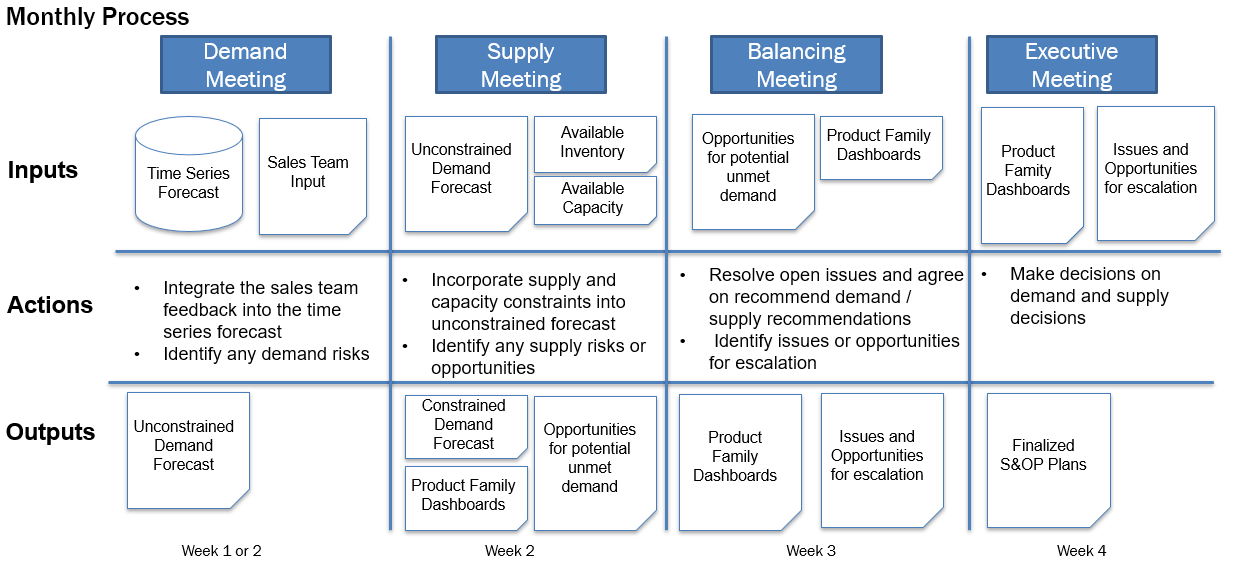



Sales Operations Planning Consulting Supply Velocity




The S Op Framework Source Thome Et Al 12 Download Scientific Diagram




Sales And Operations Planning Explorescm
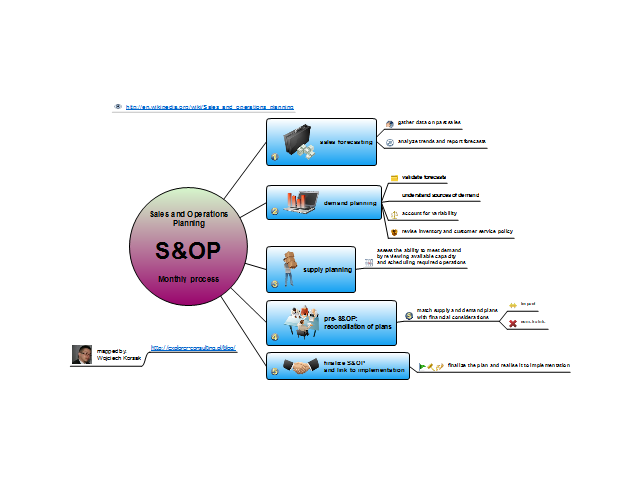



Sales And Operations Planning S Op Monthly Process Conceptdraw Biggerplate
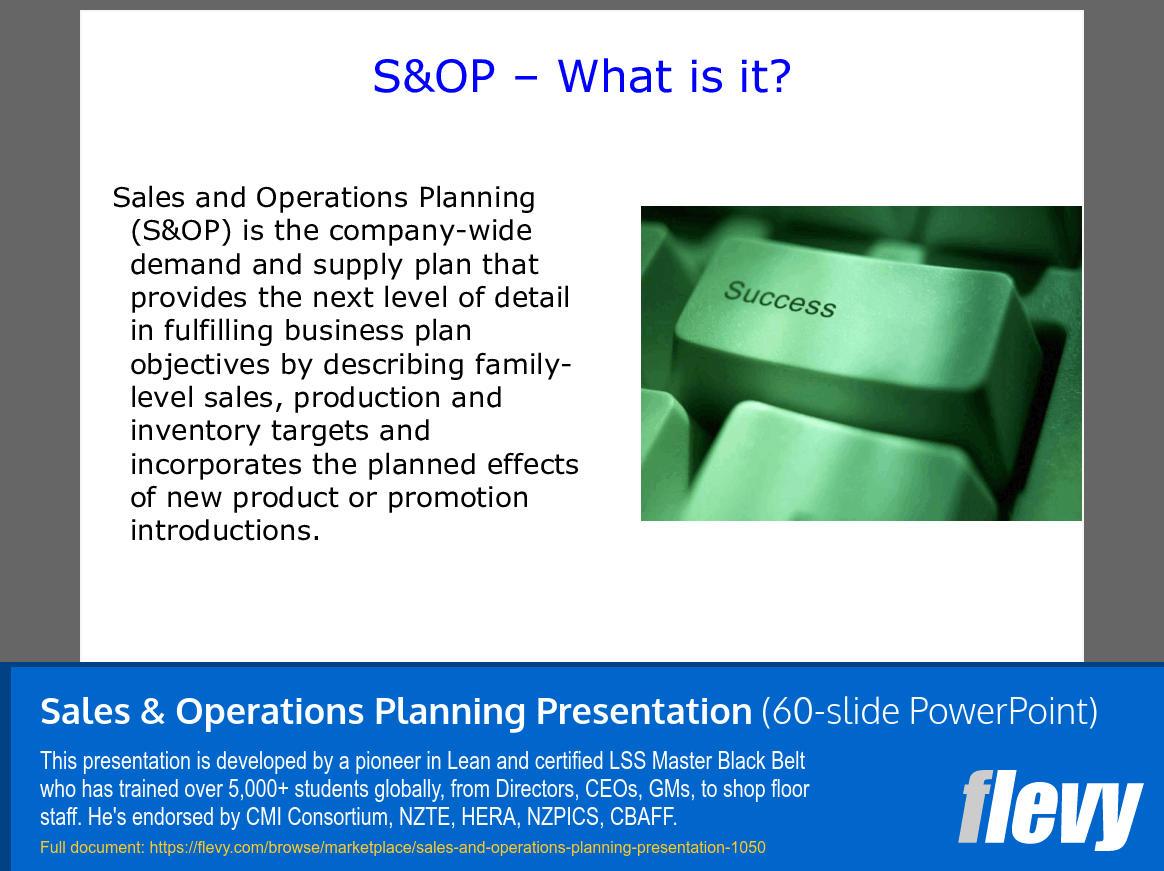



Sales Operations Planning Presentation 60 Slide Powerpoint Flevy
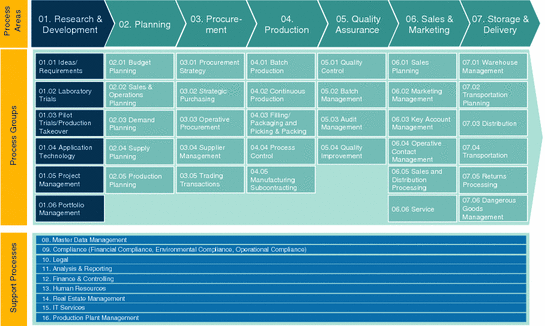



Mapping Business Processes In The Process Industry Selected Examples Springerlink



S Op Sales And Operations Planning And Sco
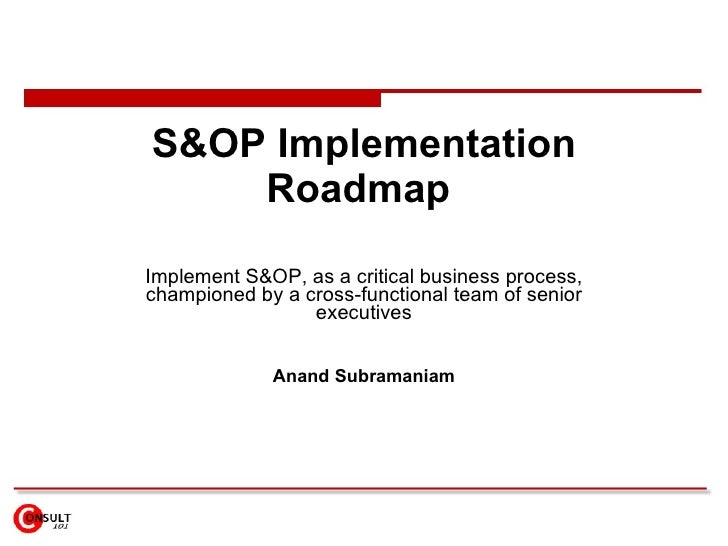



S Op Implementation Roadmap



1




S Op Five Steps To Get Started Supply Chain Shaman




The Effect Of Sales And Operations Planning S Op On Supply Chain S Total Performance A Case Study In An Iranian Dairy Company Sciencedirect




Sales Operations Planning Omnics




Sales Operations Planning Omnics




A Rudder For Course Correction July 1 09 Cscmp S Supply Chain Quarterly
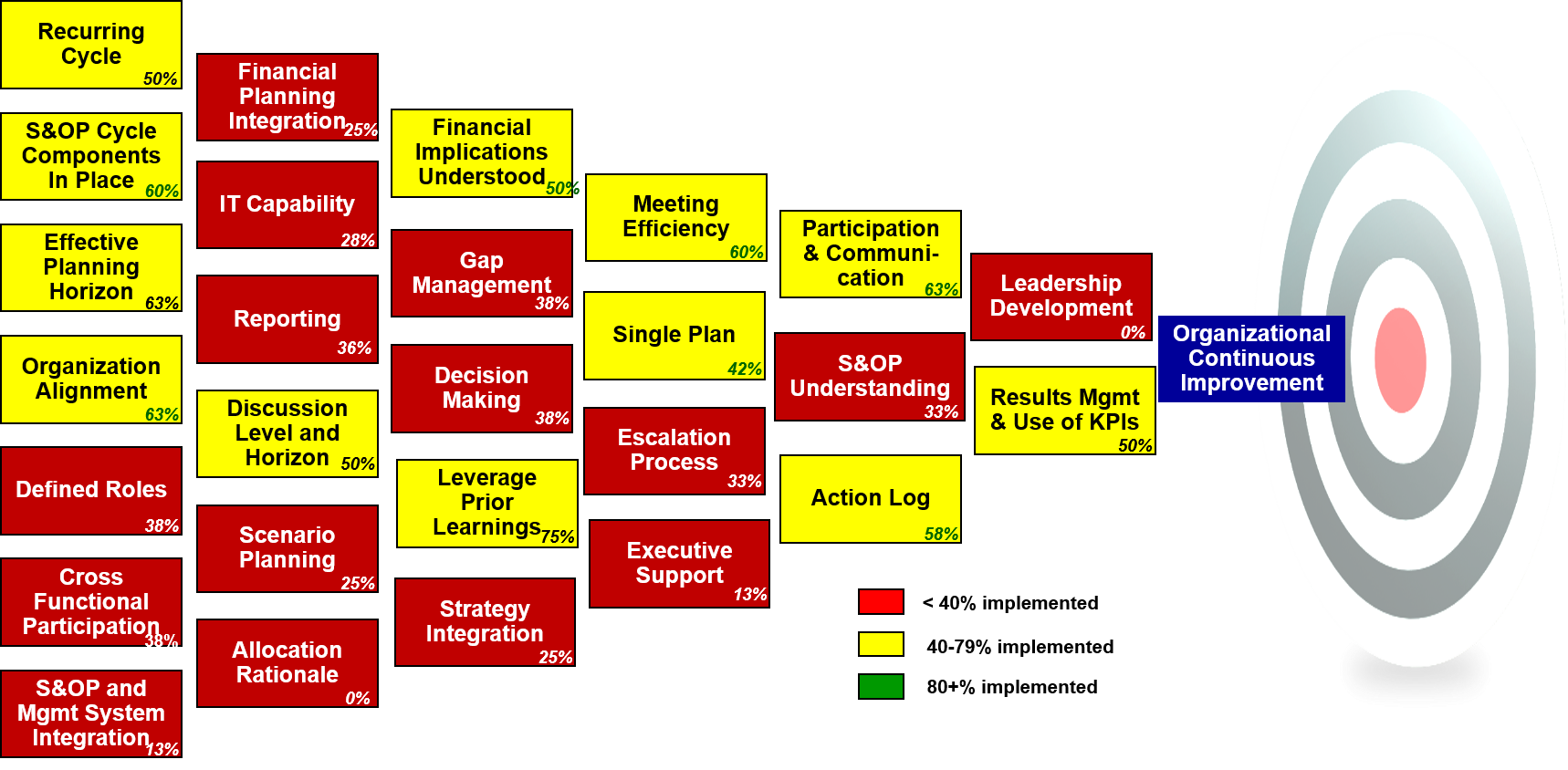



Self Assessment L Nexview Consulting S Op Consulting



2
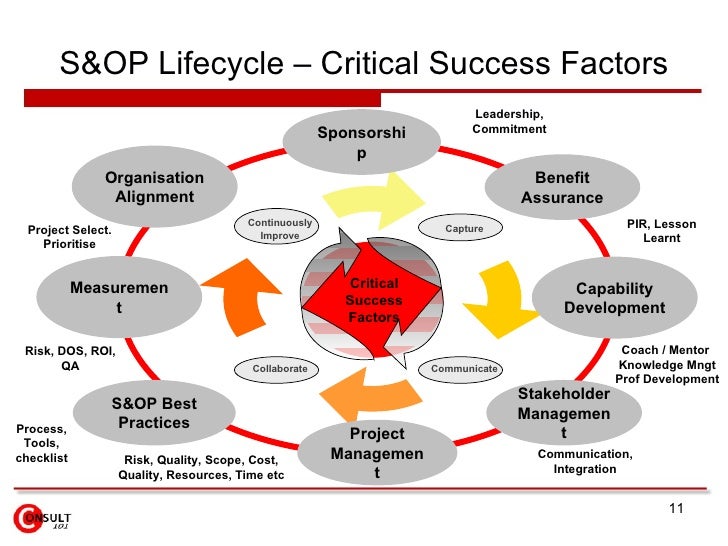



S Op Implementation Roadmap
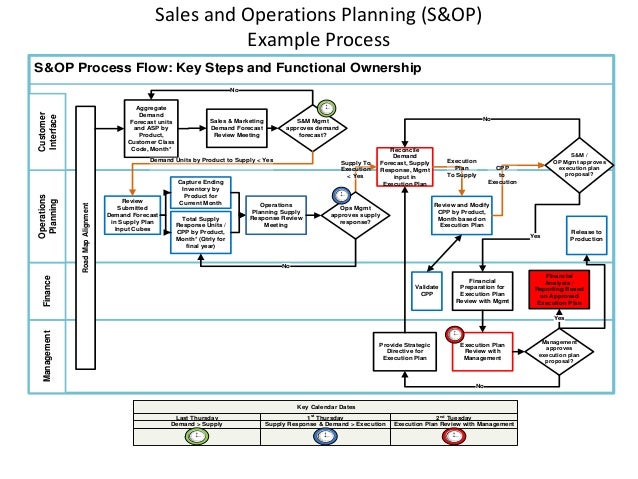



Generalized Scor Implementation




Sales And Operations Planning Powerpoint Presentation Slides Presentation Powerpoint Templates Ppt Slide Templates Presentation Slides Design Idea




The Effect Of Sales And Operations Planning S Op On Supply Chain S Total Performance A Case Study In An Iranian Dairy Company Sciencedirect




Sap Integrated Business Planning Ibp Sales And Operations Planning 18 Sap Blogs




S Op Five Steps To Get Started Supply Chain Shaman




Sap Integrated Business Planning Ibp Sales And Operations Planning 18 Sap Blogs



1
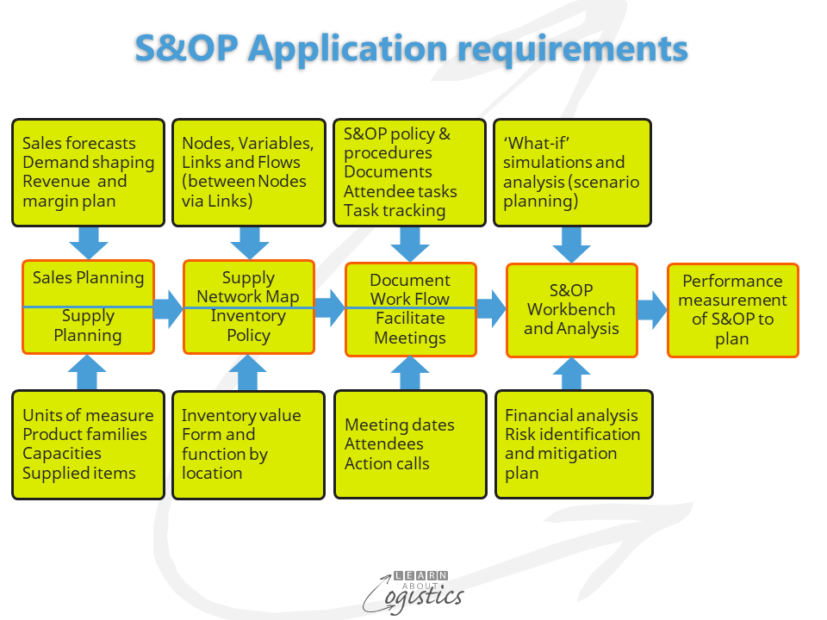



Applications Requirements That Assist S Op Decisions Learn About Logistics




Mindmap For Sales Operations Planning 2 0 Supply Chain Movement




Pi S Op Model With Centralized Sales Production And Localized Download Scientific Diagram
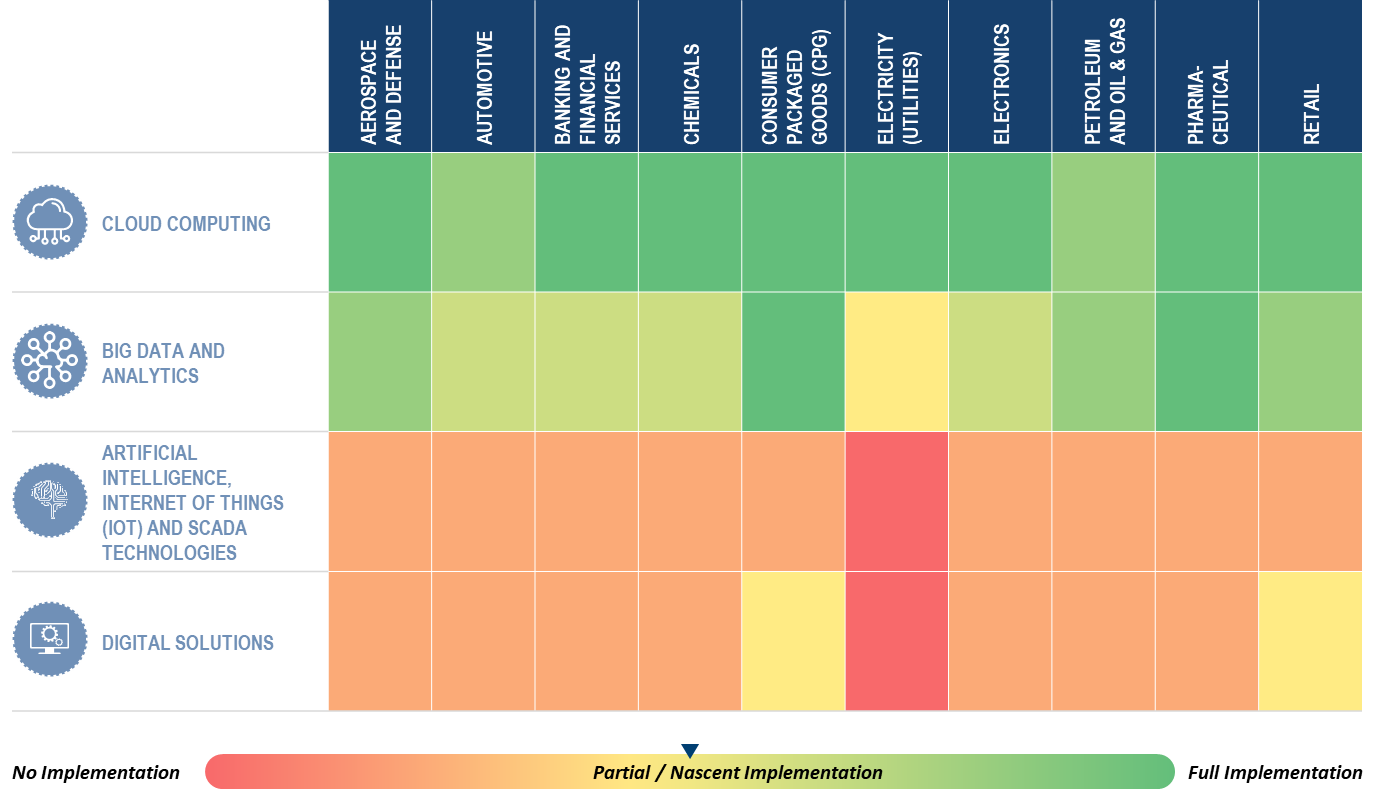



How These 6 Technologies Can Advance Your Sales Operations Planning Apqc



2




Mindmap For S Op And Ibp Supply Chain Movement
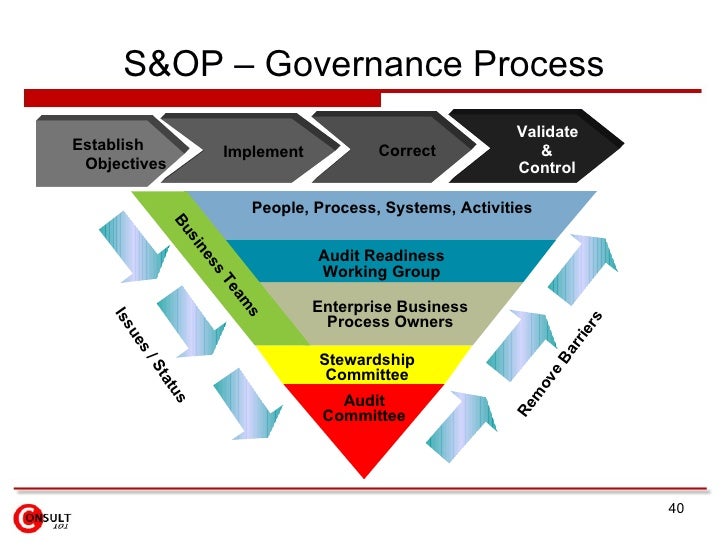



Snap S Op Process Photos On Pinterest



2
0 件のコメント:
コメントを投稿